Librixer joins project for direct recycling of “Next Generation” electric car batteries
Together with Chalmers, Volvo Cars, and other partners, the Librixer technology will be used in a project funded by Energimyndigheten to evaluate a direct, safer, and resource-efficient process to recycle spent Lithium-ion batteries, primarily production rejects and later end-of-life recycling of, from electric vehicles.
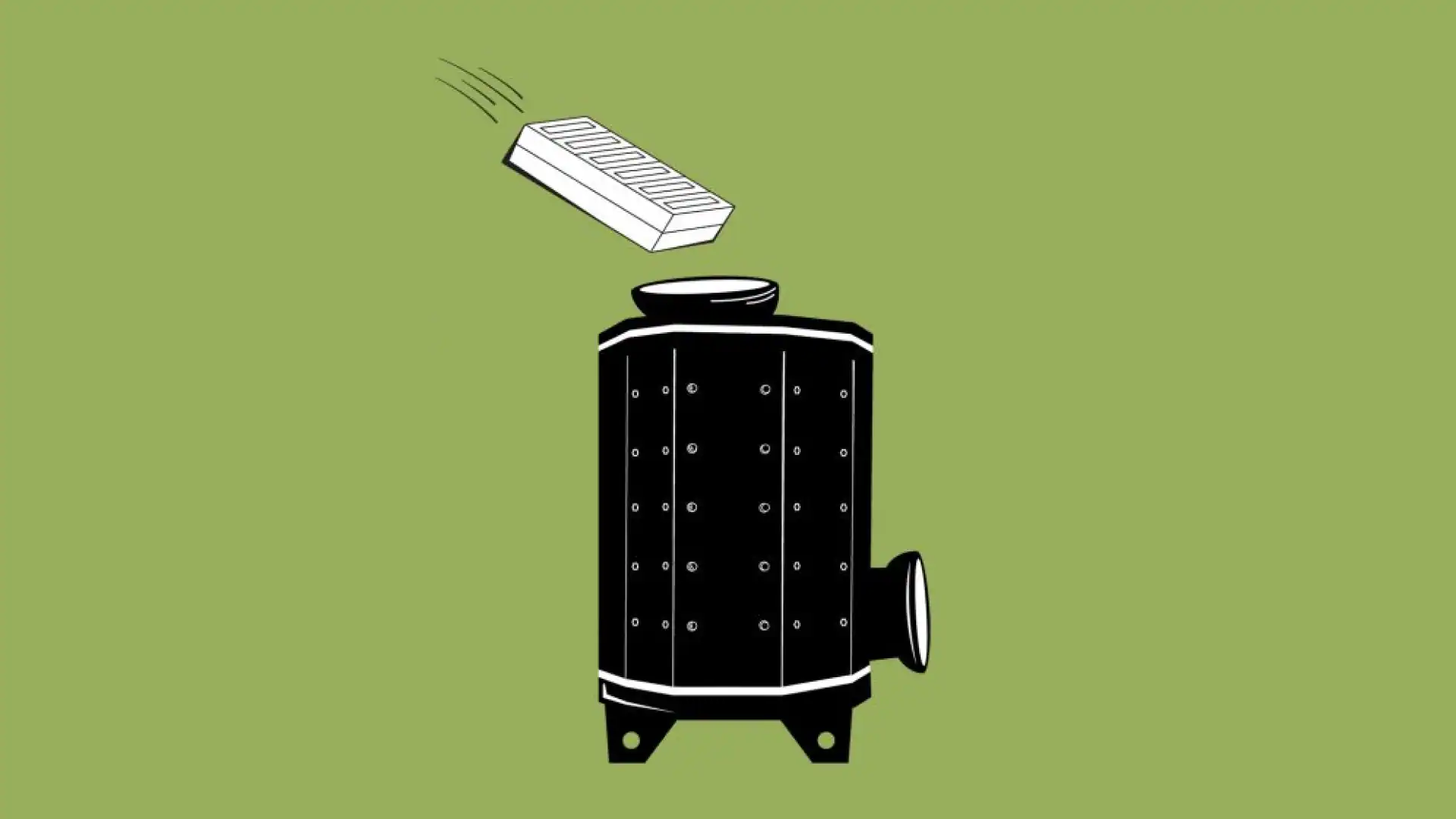
Battery demand will be a strong driver for increased availability of battery material sources – from primary and secondary sources. Since natural resources are limited, the circular economy approach plays a crucial role in reducing primary material demand and increasing the potential for waste utilization. Therefore recycling of lithium iron phosphate (LFP) in Sweden and the EU is vital to solve waste stockpiling and to decrease the pressure for mining – enabling environmental and social impacts through a greener battery value chain.
The Librixer technology will be tested for LFP cells after discharging and removal of electrolytes. The technology allows energy-efficient comminution and liberation of materials, preserving the particle structure. Thus, the technology has advantages over traditional grinding, which usually forces materials to break down through high energy, mixing components and resulting in less pure streams.
The overall goal of the project is to gather the expertise of partners from industry and academia to achieve the development of a direct, safer, and more sustainable process for the future recycling of lithium-ion batteries (LIBs) based on LFP chemistry.
Main goals of the project are:
- A direct, safer, and resource-efficient process to recycle spent LIBs based on LFP from electric vehicles, that would also be relevant to other battery applications.
- A method to recover the electrolyte and binder from LFP-LIBs, with higher efficiency compared to current alternatives (95% higher efficiency).
- Recovery of graphite – a critical raw material – and its purification for re-use in the new batteries.
- Direct recovery of cathode material and its purification for re-use in the new cells.
- A development of a greener and feasible chemical process for metallic and non-metallic constituents of the cathode material.
- Cathode precursors synthesized with recovered materials from the more sustainable recycling process proposed.
- A Life Cycle Assessment case study that demonstrates the environmental performance of each operation and of the whole process.
- Increased knowledge on greener recycling of LIBs and competence relevant to other secondary resources and battery chemistries.
- Academic goals: 3 PhD students involved, 4 master students, 6 scientific articles, 2 conference papers, and a collaborative international online seminar to reach students and researchers in Sweden and abroad.
- Knowledge sharing to stakeholders in a wider audience: dissemination of the results in reports, education materials, press releases, and traditional and social media.
The project will be structured into seven work packages and project management will be carried out by Chalmers – Industrial Materials Recycling.